Sophomore Rider
  
Currently Offline
Posts: 128
Likes: 3
Joined: Jun 1, 2013 5:11:09 GMT -5
|
Post by gingel on Jan 17, 2015 4:35:21 GMT -5
Thank you, i'll try to soak the gaskets in WD-40 and then remove them.
|
|
Sophomore Rider
  
Currently Offline
Posts: 128
Likes: 3
Joined: Jun 1, 2013 5:11:09 GMT -5
|
Post by gingel on Jan 24, 2015 4:12:28 GMT -5
Yesterday i worked on the engine head. I took out the valves and removed the valve stem seals. Did some cleaning on the head. Tried to clean the valves, but the carbon deposits on the exhaust valve are really hard to remove. I soaked the valves in a break cleaner fluid over night, and the intake valve is pretty clean, but the exhaust valve still have heavy carbon deposits on it. Is it ok to put the valve into a driver drill and then use a fine sandpaper to clean that carbon deposits? What sandpaper grit should i use? Do you have other ideas? Here is a picture of the head right after removing the valves:  The head after some cleaning:  The valves. (the exhaust valve is on the left)  
|
|
|
Post by JerryScript on Jan 24, 2015 6:46:30 GMT -5
I would try a steel brush wheel on a dremel, but your idea for the sandpaper should work. Be sure to wear gloves or hold the paper with pliers. You should change the valve stem seal on the exhaust while you're at it, it's probably pretty worn from those deposits.
|
|
|
Post by JoeyBee on Jan 24, 2015 6:50:34 GMT -5
The buckets of Chem dip they sell at auto parts stores and wal-mart may work very well. 
|
|
Sophomore Rider
  
Currently Offline
Posts: 128
Likes: 3
Joined: Jun 1, 2013 5:11:09 GMT -5
|
Post by gingel on Jan 25, 2015 9:49:00 GMT -5
I would try a steel brush wheel on a dremel, but your idea for the sandpaper should work. Be sure to wear gloves or hold the paper with pliers. You should change the valve stem seal on the exhaust while you're at it, it's probably pretty worn from those deposits. I'm replacing both of the valves stem seals (intake and exhaust). Before i'm trying to remove the carbon deposits, anyone knows what is the minimal stem diameter for the valves (for a 125cc engine)? My valves stem are around 4.  mm . what is the stem diameter for a new valve? The buckets of Chem dip they sell at auto parts stores and wal-mart may work very well.  Never seen that in stores in my area. (i'm not from the US)
|
|
|
Post by rcq92130 on Jan 25, 2015 16:08:26 GMT -5
|
|
Sophomore Rider
  
Currently Offline
Posts: 128
Likes: 3
Joined: Jun 1, 2013 5:11:09 GMT -5
|
Post by gingel on Jan 25, 2015 16:47:42 GMT -5
Yes, you are right. I will order new ones. Though SYM parts are little more expensive.
|
|
Sophomore Rider
  
Currently Offline
Posts: 128
Likes: 3
Joined: Jun 1, 2013 5:11:09 GMT -5
|
Post by gingel on Jan 31, 2015 11:40:04 GMT -5
New valves are on their way, but i wanted to try and clean the valves with a fine sandpaper. I put the valves in a driver drill, and i used a 150 and 400 grit sandpaper. Huge difference from before the cleaning as you can see from the pictures. I also measured the valves stem again with a more accurate tool, and the intake stem is 4.98mm, and the exhaust is 4.96mm. So these valves are still ok, but i'll use the new ones.  
|
|
Sophomore Rider
  
Currently Offline
Posts: 128
Likes: 3
Joined: Jun 1, 2013 5:11:09 GMT -5
|
Post by gingel on Mar 8, 2015 3:50:54 GMT -5
Hi, Just an update and also a question. The new valves arrived and i installed them, also did valve lapping. and i also replaced the springs. I was starting to assemble the engine, put the crankshaft inside (used heat & cold method), and then i went on tightening the right case. it has 2 M6 bolts.  The manual i have said to torque it to 1.5-20 kgf-m (around 15-20 Nm). So i torque it to 15Nm and one of the bolts started to break, and the other was on his way to break too.  Luckily i was able to pull them out and the threads inside the case are ok. After when searching in google i found a chart saying that M6 bolts in aluminum needs around 5 ft/lb (around 7Nm). What do you think is the correct torque for the M6 bolts? There are also the 2 M6 bolts on the left side of the engine head (where the timing) . What is the correct torque for them? The manual is saying 1.0-1.4 kgf-m (around 10-14 Nm). Is it too much?
|
|
|
Post by geh3333 on Mar 9, 2015 1:00:04 GMT -5
Its good to torque them to the correct specs , TBA I just tighten them until they feel nice and tight . it is very easy to over tighten these bolts and strip them . to be safe u can use some thread lock and tighten them until they seem snug , then go just a little further . the thread lock will keep them nice and tight. You can usually tell what is tight enough with these engine bolts. Just my opinion.
|
|
Sophomore Rider
  
Currently Offline
Posts: 128
Likes: 3
Joined: Jun 1, 2013 5:11:09 GMT -5
|
Post by gingel on Mar 10, 2015 18:54:00 GMT -5
Thank you for the advice. At the end i tightened them until it felt tight enough. I hope to post more pictures very soon.
|
|
Sophomore Rider
  
Currently Offline
Posts: 128
Likes: 3
Joined: Jun 1, 2013 5:11:09 GMT -5
|
Post by gingel on Mar 13, 2015 12:19:28 GMT -5
I wanted to ask regarding the piston rings installation. I found a video on youtube that explain how to do it. Is this the correct way?
Thank you.
|
|
|
Post by JerryScript on Mar 13, 2015 16:01:43 GMT -5
Yes, that is a good video. Only thing I do different is clock the oil rings 120* apart from each other, I don't like the idea of the gaps being so close. One hint, this guy had no problems getting the piston and rings into the jug, it's not that easy when it's all installed in the engine. I use a hose clamp to compress the rings, put the top of the piston into the jug, then tap the jug down forcing the hose clamp off as the rings slide into the jug. No cuts on your fingers with this method.
|
|
|
Post by geh3333 on Mar 13, 2015 16:29:03 GMT -5
Yes, that is a good video. Only thing I do different is clock the oil rings 120* apart from each other, I don't like the idea of the gaps being so close. One hint, this guy had no problems getting the piston and rings into the jug, it's not that easy when it's all installed in the engine. I use a hose clamp to compress the rings, put the top of the piston into the jug, then tap the jug down forcing the hose clamp off as the rings slide into the jug. No cuts on your fingers with this method. TBA when I did my bbk , I had no issue what so ever with inserting the piston and rings into the jug . maybe I just got lucky ? Either way I'm sure your method works very good and if I ever have issues in the future I will def use it.
|
|
Sophomore Rider
  
Currently Offline
Posts: 128
Likes: 3
Joined: Jun 1, 2013 5:11:09 GMT -5
|
Post by gingel on Mar 13, 2015 20:01:31 GMT -5
Yes, that is a good video. Only thing I do different is clock the oil rings 120* apart from each other, I don't like the idea of the gaps being so close. One hint, this guy had no problems getting the piston and rings into the jug, it's not that easy when it's all installed in the engine. I use a hose clamp to compress the rings, put the top of the piston into the jug, then tap the jug down forcing the hose clamp off as the rings slide into the jug. No cuts on your fingers with this method. Do you mean the 3 bottom rings (the spring with the 2 oil rings) ? I thought you need to put the oil rings gap 20mm on each side of the spring gap. it's not supposed to be like in this picture? 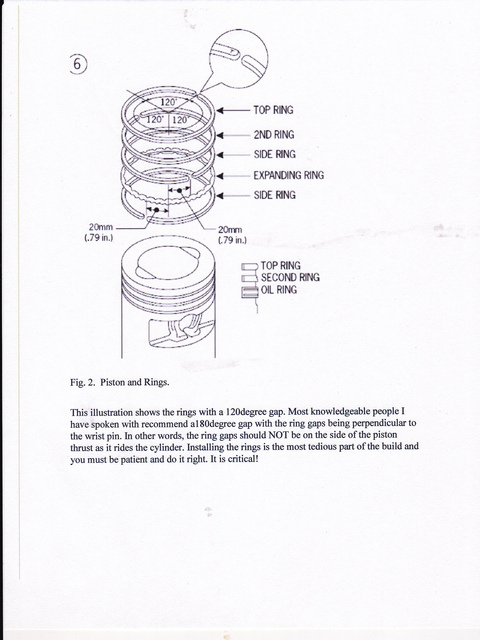
|
|