|
Post by triker on May 18, 2014 12:47:37 GMT -5
I' m guessing he didn't get the magneto bolts tight, one or more came loose and the flywheel hit it.
Roy
|
|
|
Post by triker on May 18, 2014 1:30:43 GMT -5
was the shroud on the engine? If so I can't understand how the magneto fell off and rolled down the street, unless it broke up the shroud when the crank broke.
Roy
|
|
|
Post by triker on May 18, 2014 1:18:57 GMT -5
He may have an auxiliary tank that he attaches the fuel hose to, or he may just fill the carb. float bowl. Engines will run a few minutes with the fuel in the float bowl before it runs out.
Roy
|
|
|
Post by triker on May 15, 2014 23:42:41 GMT -5
My 50cc mojo came with a tow ball installed. I can't remember what the capacity is though. Our trikes don't lean like the two wheelers do, so a regular ball and hitch will work.
Roy
|
|
|
Post by triker on Apr 4, 2014 11:57:29 GMT -5
The cases I have are identical except for the position of the pump locator dowel holes. I don't know if this is true for all pumps and cases. it probably varies depending on manufacturers. either pump can be used if you change the gears. You can just drill out the correct holes for the dowels or just not use them. 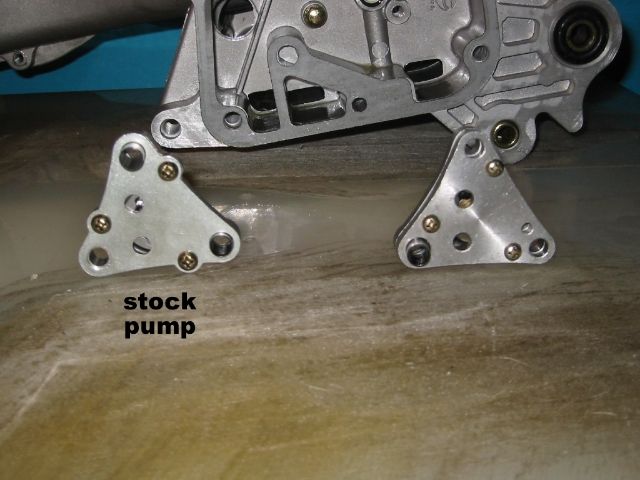 The pump on the left is the stock 22/47 pump and the one on the right is a 16/33 pump. notice where the dowels are located. 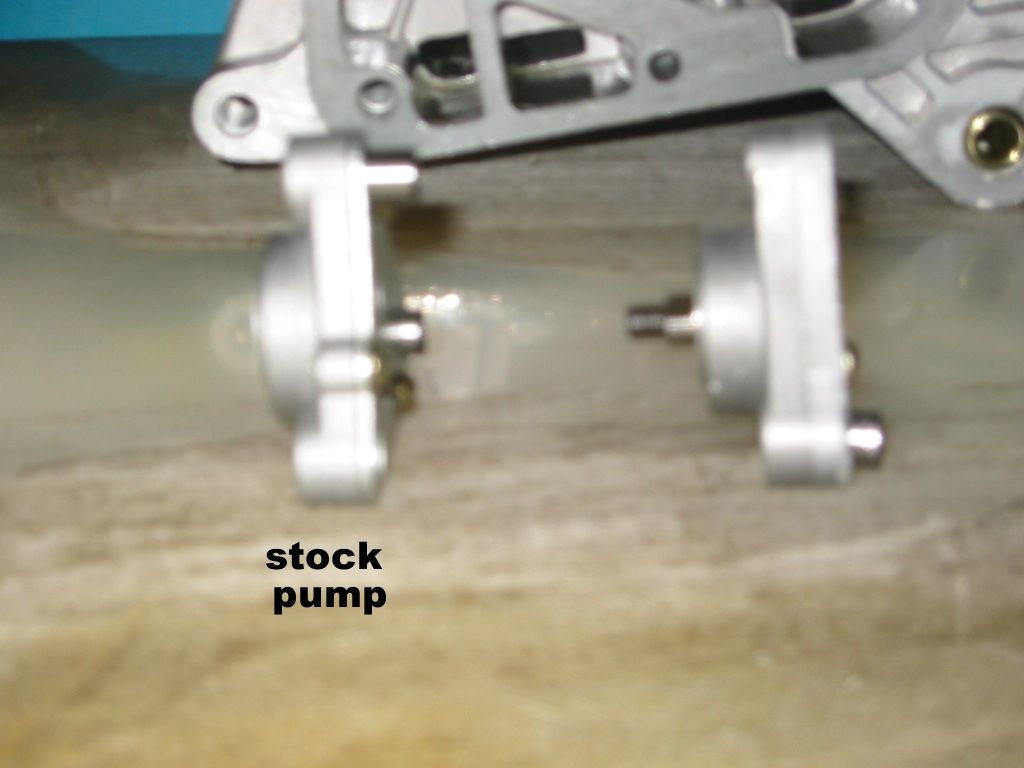 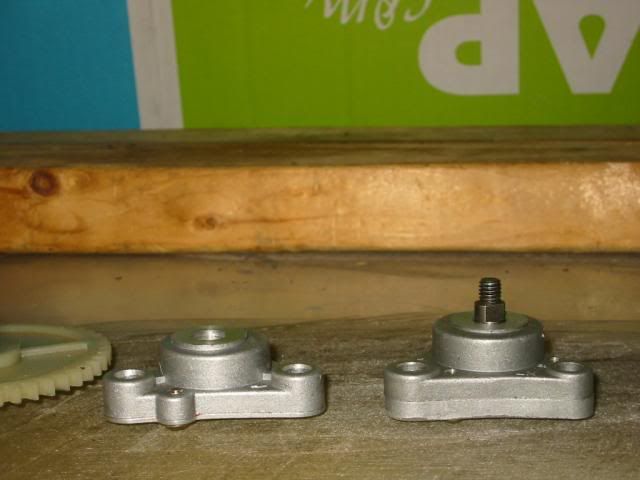 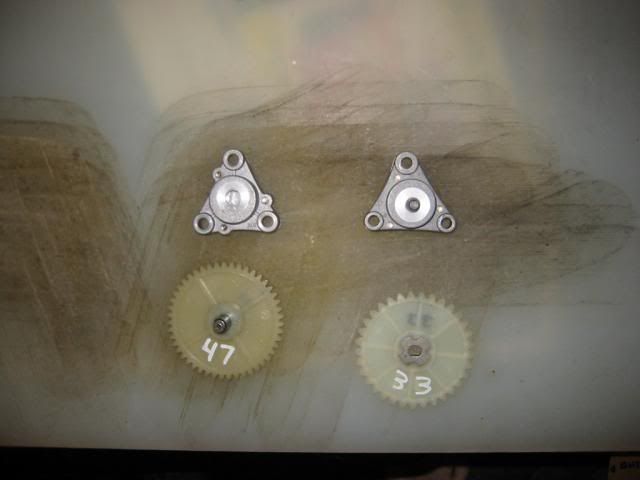 I preferred to use the stock 22/47 pump because the shaft is supported in a hole in the outer case, the 16/33 pump does not use this support. Roy
|
|
|
Post by triker on Apr 4, 2014 2:38:35 GMT -5
There are two different oil pumps for a 139qmb engine. One pump uses a 47 tooth driven gear and a 22 tooth drive gear on the crankshaft. The second pump uses a 33 tooth driven gear and a 16 tooth drive gear on the crankshaft. The first pump turns at a ratio of 1:2.1363 and has internal gears that are 10mm thick. the second pump turns at a ratio of 1:2.0625 and has internal gears that are 8mm thick. The first pump has thicker gears and would move a greater volume of oil if both pumps turned at the same ratio. The drive gears on these two pumps are not interchangeable. I have taken the shaft out of a 47 tooth gear and machined the hub that was imbedded into the plastic gear off. I then bored the hole in the center of a 33 tooth gear and pressed it onto the machined shaft. The crankshaft I have has a 16 tooth drive gear and I can now use the pump with thicker gears turning at the faster ratio of 1:2.0625. This should increase oil flow volume and pressure. I have not tested this yet, but I will do a test on oil flow volume and pressure at given rpms for the two stock pumps and the pump with the modified gears. Also The 16/33 pumps I have have the locator dowel pins in different locations. I could still use these pumps without the locator pins but must make sure the pump is in the correct position so the ports are open and the gears mesh properly.
Roy
|
|
|
Post by triker on Sept 29, 2013 14:11:43 GMT -5
The Bearing you should have is a 6303-2/p6, it measures 17mm I.D x 42mm O.D. x 12mm thick. This is a non sealed open bearing.
The replacement bearing you got is is probably a 6303- 2RS, It measures 17mm I.D x 47mm O.D. x 14mm thick. This is a rubber or plastic sealed bearing on both sides or double sealed. A 6303zz bearing measures the same as the 6303-2RS but uses steel shields instead of rubber or plastic.
As you can see both bearings are 6303 but are different sizes. The 6303-2/P6 bearing is probably a chinese made bearing and are not standard size bearings.
Roy
|
|
|
Post by triker on Aug 16, 2013 21:48:25 GMT -5
I must be missing something and I have been around quite awhile and have fixed many chains probably more than most but a "SWELLING TOOL"? Can someone put a picture of this tool. I know there are many types of chain breakers, installers, peeners and spreaders but I have never heard of a tool called a "SWELLING TOOL". The only one I know of is what boxers use to get their swells down by pressing a cold piece of hand held metal which they do call swelling tool. Alleyoop I have probably repaired or replaced more chain in a month than you have seen in your life, and probably some types of chain you don't even know about. I have been a machine mechanic for almost 30 years. I am not going to take my camera to work and take photos of my tools just to prove to you that these tools do exist. They call these tools by a number of names, just like a lot of other tools. I am not going to argue with you on this subject any more. If you don't believe they make this kind of tool research it. Roy
|
|
|
Post by triker on Aug 15, 2013 1:13:30 GMT -5
I have looked at many cam chains. Every one I have has a different colored link, that is the connecting link. It is possible to put a cam chain back together with out using a welder, you just need the right tool. I use a swelling tool at work to make continuous chain without a master link that uses a clip. The tool I use is called a swelling tool. It swells or peens the pins just like at the factory. The one I have works on chain sizes #25-#60. Here is a photo of the cam chain on my workbench. It is possible to replace this link with the proper tools. 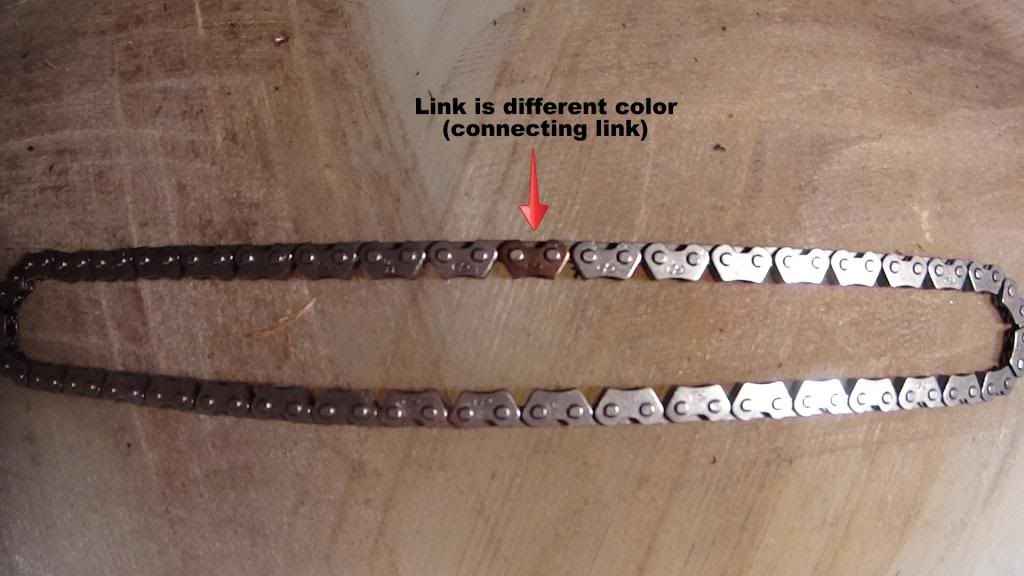 Roy
|
|
|
Post by triker on Aug 14, 2013 12:41:29 GMT -5
And I just break the old chain at the joining link (if it is not already broken), tie it to the old chain which I break at the joining link and using the old chain to just pull the new one through re-joining the ends when I am done. All done just by removing just the valve cover, rockers and cam shaft. A couple of questions. I know how to break chains apart and have several size chain breakers. Do you use a new link and peen the pins when you re- connect the chain or do you reuse the link you broke, if so what tool do you use to re-peen the pins? Roy
|
|
|
valve lash
by: triker - Aug 11, 2013 21:11:52 GMT -5
Post by triker on Aug 11, 2013 21:11:52 GMT -5
If you set the valve lash at the proper timing marks with cylinder at top dead center, then you turn the crank in the proper direction one full turn and the gap gets larger you have something wrong. As at that point the exhaust valve should be just about to close and the intake valve just about to open. There should not be a larger gap on either valve at that point.
Roy
|
|
|
Post by triker on Aug 11, 2013 0:08:54 GMT -5
I think he is referring to the after market oil catch can that uses a hose that replaces the oil dip stick. In my opinion these are a waste of money. If your engine crank case is developing more pressure than the stock PCV valve can release than you have something wrong. The piston rings were not installed properly, they are not seated, or the end gap is to large ect.. The crank case does build quite a bit of pressure even if everything is proper. But the stock PCV valve should relieve enough, if it does not check the valve. I have never had a problem with crankcase pressure and do not lose any oil through the PCV valve
Roy
|
|
|
Post by triker on Aug 10, 2013 0:26:16 GMT -5
It may work out however with the plastic gears you are taking a chance that the increased pressure can can cause them to strip driving the higher volume pump faster then it was originally setup to run. This will be more of an issue if you are running oil thicker than specified for your climate or if you don't allow the engine to warm up a bit before starting off. These plastic gears are very tough. The extra stress, if any the little bit thicker gears in the oil pump will be minimal. I do not think it will be a problem. Roy
|
|
|
Post by triker on Aug 10, 2013 0:21:25 GMT -5
WHY? were you having a problem?the gains you would get are negligible for the amount of oil in the sump. I would just leave well enough alone JMO No, I am not having a problem. I am just trying to figure a way to move more oil so that in the future I may just try to install an oil cooler. I have as yet to see an engine that didn't benefit from a higher oil flow. Even with a small amount of oil in the sump the oil still removes heat from the engine parts. You can leave well enough alone if you want to, not me. New and better stuff would never be found if everybody just left well enough alone. Roy
|
|
|
Post by triker on Aug 9, 2013 1:47:48 GMT -5
There are two different oil pumps for a 139qmb engine. One pump uses a 47 tooth driven gear and a 22 tooth drive gear on the crankshaft. The second pump uses a 33 tooth driven gear and a 16 tooth drive gear on the crankshaft. The first pump turns at a ratio of 1:2.1363 and has internal gears that are 10mm thick. the second pump turns at a ratio of 1:2.0625 and has internal gears that are 8mm thick. The first pump has thicker gears and would move a greater volume of oil if both pumps turned at the same ratio. The drive gears on these two pumps are not interchangeable. I have taken the shaft out of a 47 tooth gear and machined the hub that was imbedded into the plastic gear off. I then bored the hole in the center of a 33 tooth gear and pressed it onto the machined shaft. The crankshaft I have has a 16 tooth drive gear and I can now use the pump with thicker gears turning at the faster ratio of 1:2.0625. This should increase oil flow volume and pressure. I have not tested this yet, but I will do a test on oil flow volume and pressure at given rpms for the two stock pumps and the pump with the modified gears.
Roy
|
|